AIRPULL INTERNATIONAL INDUSTRIAL CO.,LTD

AFTER INSTALLING AN OIL-GAS SEPARATOR, THE CUSTOMER REPORTED OIL LEAKAGE. WHAT SHOULD BE DONE?
After the customer completed the installation of the oil-gas separator, they immediately reported an abnormal oil leakage issue. To address this problem, the service team responded swiftly, replacing three brand-new oil-gas separators in succession. However, the oil leakage issue remained unresolved. This challenging situation prompted immediate attention, with technical engineers rushing to the site to conduct a thorough investigation and analysis.
Upon arrival at the site, the technical engineers first conducted a comprehensive monitoring of the equipment’s operational parameters and carefully inspected the installation status of the oil-gas separator and the condition of the piping connections, initially ruling out the possibilities of improper installation or external piping leaks. Subsequently, the engineers disassembled and inspected each critical component of the oil-gas separation system. After a series of rigorous and meticulous testing and verification procedures, the root cause of the issue was finally identified: the return oil check valve was experiencing a bidirectional air leakage fault.
Under normal conditions, the return oil check valve should have unidirectional flow characteristics, allowing return oil from the compressor head to flow along the designated path into the system oil circuit, ensuring normal lubricant circulation and replenishment. However, in this case, the check valve lost its intended blocking function, resulting in a bidirectional flow state. This fault caused the engine oil, which should have circulated normally, to abnormally flow back into the oil-gas separation tank. Due to the disrupted oil return path, a large amount of lubricating oil could not participate in the circulation process as intended and instead accumulated abnormally within the oil-gas separation tank, ultimately leading to severe oil leakage.
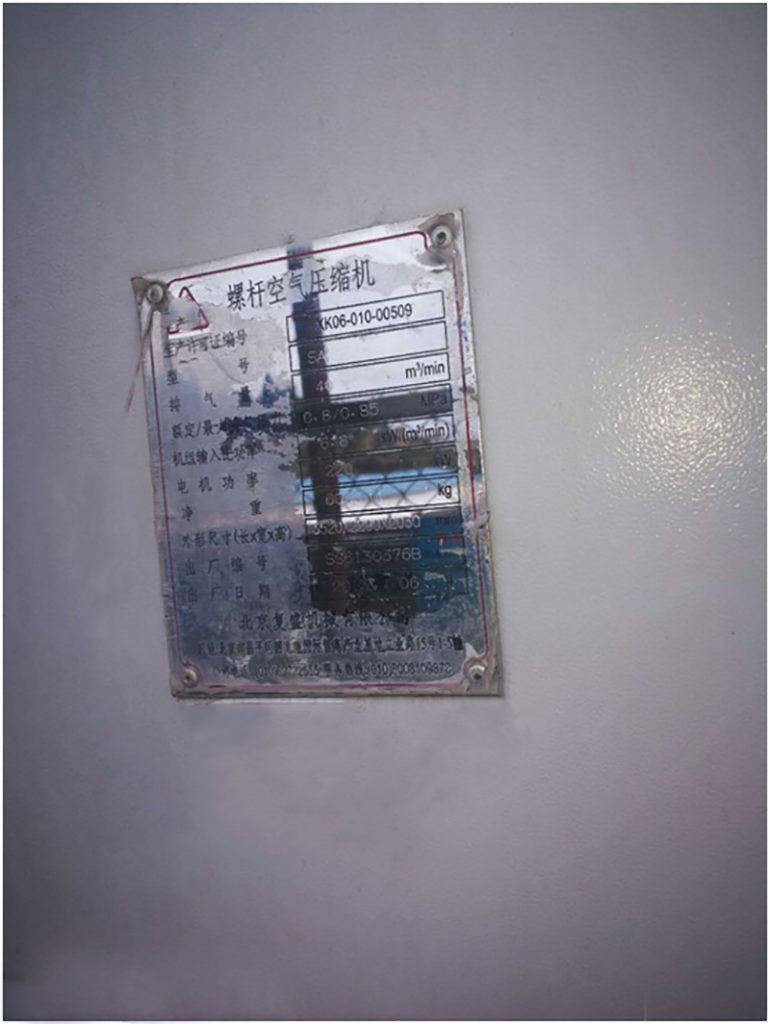
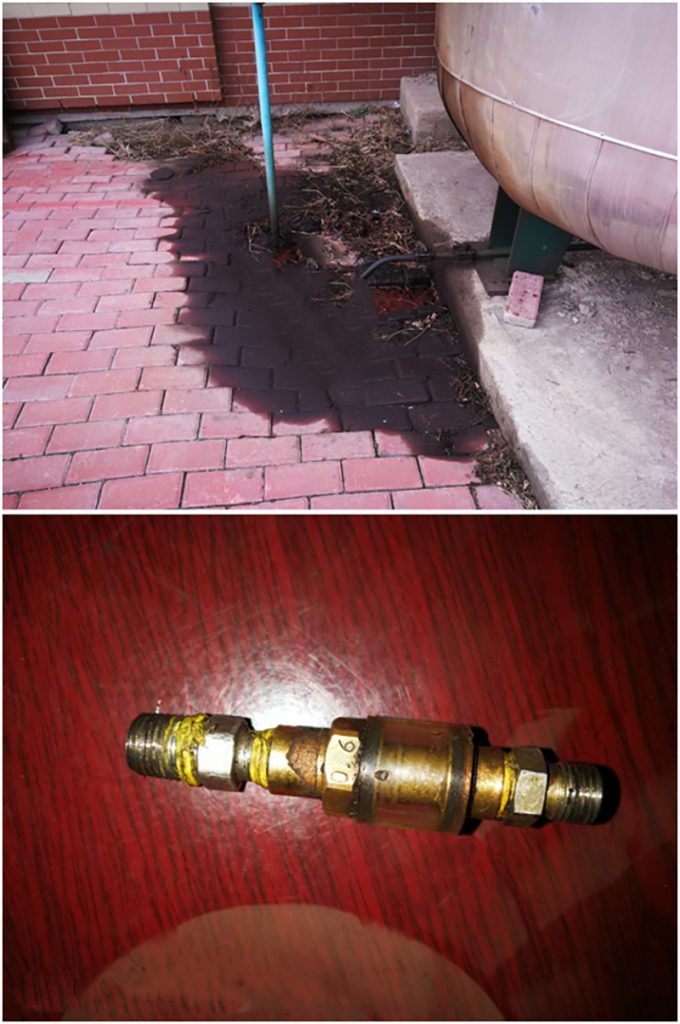
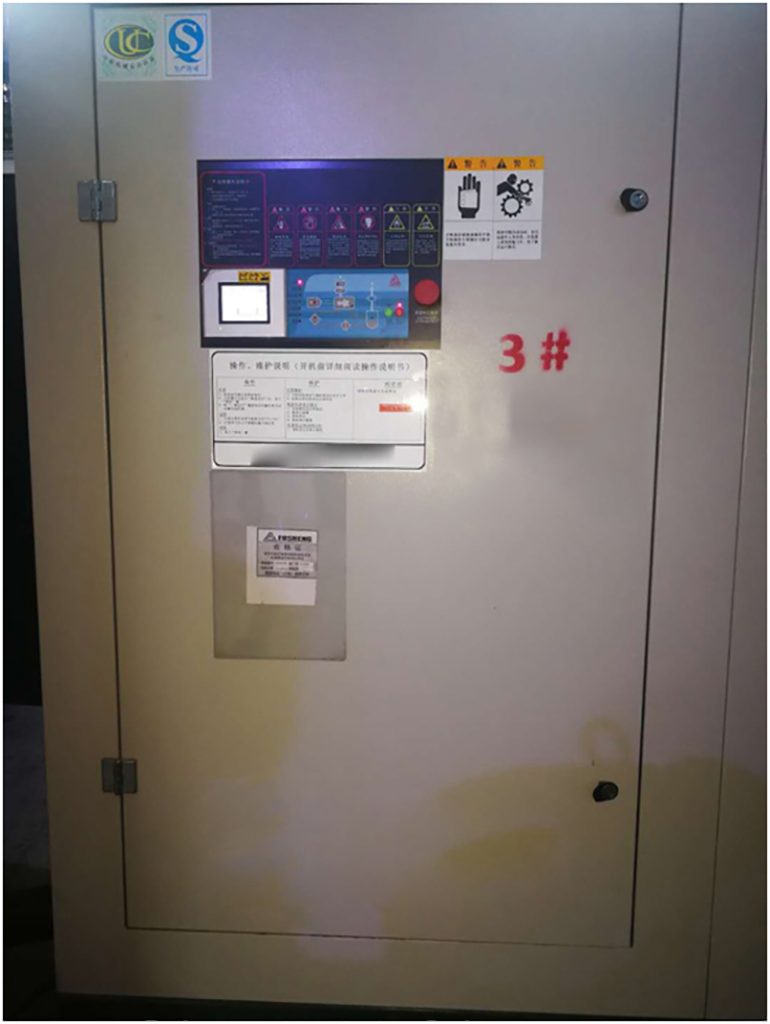